Les grandes tendances de l’automatisation industrielle en 2025
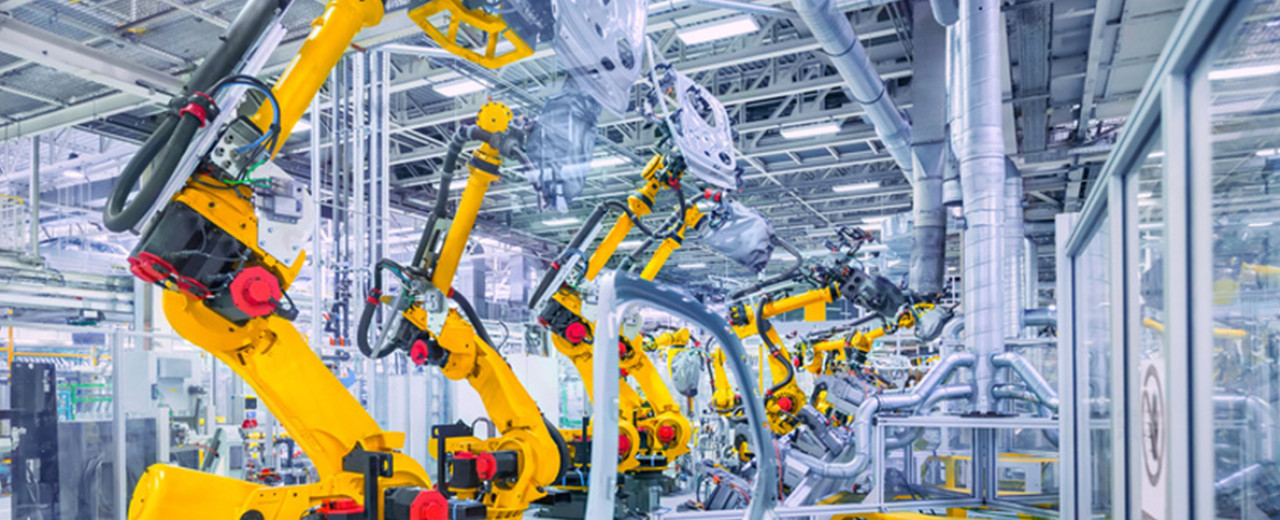
L’automatisation industrielle connaît une transformation radicale, portée par la convergence de la robotique avancée, de l’IoT omniprésent et de l’IA prédictive. Ces technologies redéfinissent l’efficacité opérationnelle, notamment dans la gestion des fluides et lubrifiants, où précision et connectivité deviennent critiques. Pour les acteurs industriels, maîtriser ces évolutions n’est plus un avantage concurrentiel, mais une nécessité pour rester compétitif dans un marché exigeant flexibilité et durabilité.
L’ère de l’industrie connectée : connectivité et intelligence
Robotique collaborative et autonome
Les robots nouvelle génération intègrent des capteurs haute résolution et l’apprentissage machine pour s’adapter dynamiquement aux tâches complexes. En 2025, leur déploiement explose dans les chaînes de montage, avec :
-
Des cobots capables d’auto-optimiser leurs trajectoires en temps réel.
-
Des systèmes mobiles autonomes (AMR) gérant la logistique intra-usine sans supervision humaine.
IIoT : colonne vertébrale de l’usine connectée
L’Internet Industriel des Objets crée un écosystème unifié où machines, outils et capteurs communiquent en continu. Les bénéfices clés incluent :
-
La surveillance en temps réel de l’état des équipements (température, vibration, usure).
-
L’anticipation des pannes via l’analyse des données de télémétrie.
IA prédictive : de la réactivité à la proactivité
L’intelligence artificielle dépasse la simple analyse pour devenir prescriptive. Elle transforme la maintenance et la production grâce à :
-
Des algorithmes prédisant l’usure des outils avec 98% de précision.
-
L’optimisation autonome des paramètres d’usinage (vitesse, lubrification) pour maximiser le rendement.
Révolution dans la gestion des fluides : la microlubrification intelligente
Les limites des systèmes traditionnels
Les méthodes classiques de lubrification génèrent des coûts cachés majeurs :
-
Surconsommation de fluides : Jusqu’à 50% de gaspillage avec les systèmes par arrosage.
-
Coûts environnementaux : Traitement complexe des fluides usagés et émissions de CO₂ accrues.
-
Pannes imprévues : Sous-lubrification entraînant une usure prématurée des outils.
La microlubrification (MQL) : précision et économie
Cette technologie applique des micro-quantités de lubrifiant directement à la zone de contact outil/pièce. Les gains sont tangibles :
-
Réduction de 70% des coûts de lubrifiants grâce à un dosage millimétré.
-
Amélioration de la qualité : Pièces usinées propres, sans résidus de fluide.
-
Durabilité renforcée : Prolongation de 30% de la durée de vie des outils.
Une étude SKF révèle que "La MQL abaisse le coût total du cycle de vie de 54% comparé aux méthodes traditionnelles."
Intégration IIoT et MQL : le duo gagnant
Les centrales de microlubrification modernes, comme les solutions HPM Technologie, intègrent nativement l’IIoT pour :
-
Réguler le débit de lubrifiant en fonction des données de l’usinage (matériau, vitesse).
-
Générer des alertes préventives lorsque les réservoirs atteignent un seuil critique.
-
Centrales de microlubrification HPM : cœur des usines 5.0
Architecture modulaire pour une flexibilité maximale
Les centrales HPM s’adaptent à tout environnement, des ateliers de mécanique aux lignes d’assemblage aérospatial. Leurs atouts :
-
Réservoirs pressurisés : Gestion de fluides jusqu’à 2 300 mm²/s de viscosité.
-
Connexions multiples : Jusqu’à 60 buses pilotées par une seule centrale.
-
Comptabilité IIoT : Intégration transparente avec les MES (Manufacturing Execution Systems).
Contrôle intelligent et maintenance prédictive
Les systèmes HPM intègrent des capteurs qui transforment la lubrification en processus data-driven :
Surveillance en temps réel de la pression et du débit.
Algorithmes d’IA prédisant les besoins en maintenance (ex : colmatage des buses).
Réduction des coûts opérationnels
-
Économie d’énergie : Jusqu’à 90% de réduction de la consommation d’air comprimé vs. les systèmes classiques.
-
Maintenance simplifiée : Pas de pièces mobiles, remplacement rapide des filtres.
Étude de cas : gains tangibles avec les solutions HPM
Réduction des coûts chez un équipementier automobile
Après l’installation de centrales HPM sur ses lignes d’usinage, un constructeur a observé :
-
40% de baisse des dépenses en lubrifiants.
-
25% d’augmentation de la durée de vie des fraises.
-
Élimination des arrêts machines liés aux défauts de lubrification.
Intégration avec l’écosystème numérique
Les centrales HPM communiquent avec les ERP via des API standardisées, permettant :
-
La réorganisation automatique des approvisionnements en fluides.
-
L’ajustement en temps réel des paramètres pour chaque lot de production.
L’automatisation comme levier de compétitivité
L’automatisation industrielle en 2025 transcende la simple mécanisation. Elle fusionne intelligence artificielle, connectivité omniprésente et gestion optimisée des ressources pour créer des usines agiles, durables et économes. La microlubrification intelligente, incarnée par les centrales HPM, y joue un rôle pivot en éliminant les gaspillages tout en garantissant une qualité irréprochable.
Prêt à aller plus loin dans votre démarche d’optimisation ?
Découvrez tous les produits de nos gammes de centrales de microlubrification.
Consultez les autres articles de notre blog.
Contactez nos experts pour des conseils avisés et un accompagnement personnalisé :
-
✉️ contact@kermaz-pneumatic.com
-
☎️ 01 69 30 69 80