La microlubrification : Une solution éco-responsable pour l’usinage industriel
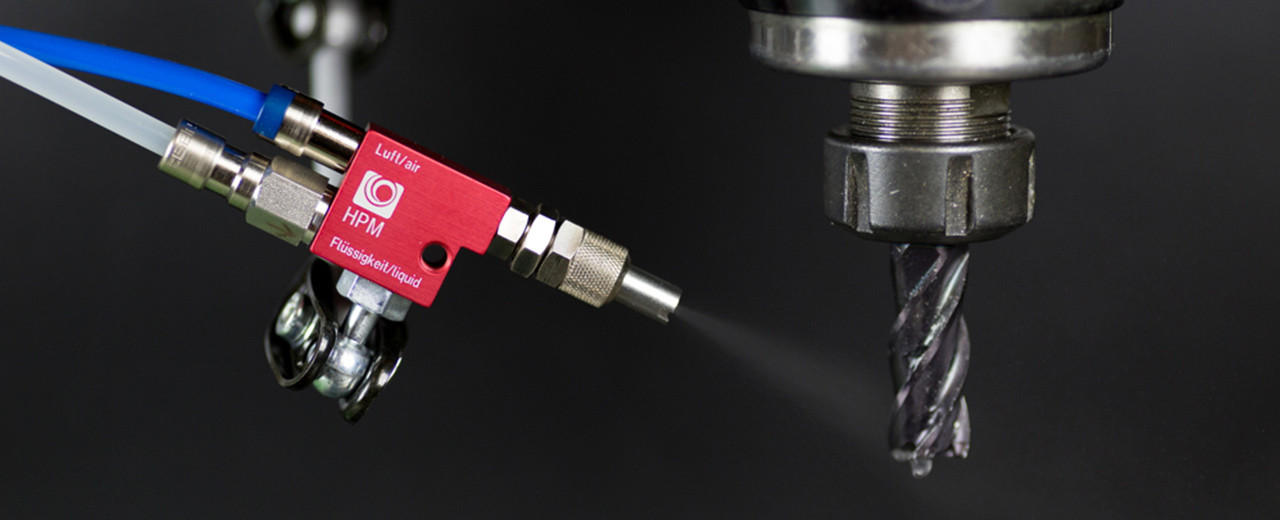
Face à la pression croissante pour réduire l’empreinte environnementale des ateliers et optimiser la rentabilité des opérations, l’usinage industriel doit se réinventer. La microlubrification, ou MQL (Minimum Quantity Lubrication), s’impose aujourd’hui comme une technologie de rupture, capable de transformer les process d’usinage tout en répondant aux exigences de performance, de sécurité et de responsabilité sociétale.
Qu’est-ce que la microlubrification (MQL) ?
Définition et principe de fonctionnement
La microlubrification consiste à appliquer, à l’aide d’une centrale de microlubrification, une quantité très réduite de lubrifiant précisément là où cela est nécessaire, sous forme de microgouttelettes, directement sur la zone de coupe ou d’usinage. Ce procédé repose sur l’utilisation de buses de haute technicité, capables de micro-pulvériser le fluide sur des surfaces planes ou tridimensionnelles, en minimisant le gaspillage et la pollution.
Comment fonctionne une centrale de microlubrification ?
-
Un réservoir (de 1 à 25 litres selon les modèles) stocke le lubrifiant.
-
L’air comprimé, filtré et régulé, entraîne le lubrifiant vers les buses.
-
Le mélange air/lubrifiant est atomisé en microgouttelettes, ciblant la zone d’usinage.
-
La quantité de lubrifiant et le débit d’air sont réglables pour s’adapter à chaque opération (perçage, fraisage, sciage, etc.).
Les contraintes de la lubrification traditionnelle en usinage
Avant d’adopter la microlubrification, il est essentiel de comprendre les limites des systèmes classiques, qui génèrent des coûts et des contraintes souvent sous-estimés :
-
Consommation excessive de lubrifiant et d’eau : Les systèmes à lubrification conventionnelle utilisent des volumes de fluides très important, générant des déchets à traiter et des coûts de gestion élevés.
-
Problèmes de propreté et de sécurité : Les sols sont souvent souillés, augmentant le risque de glissades, de corrosion ou de contamination des pièces.
-
Maintenance lourde : Gestion des vidanges, nettoyage des machines, recyclage ou traitement des fluides usagés.
-
Risques sanitaires : Présence de brouillards d’huile, de bactéries et de champignons dans les émulsions, exposition des opérateurs à des substances nocives.
-
Difficulté à maîtriser les coûts cachés : Temps d’arrêt pour nettoyage, usure prématurée des outils, gestion complexe des déchets.
Les avantages de la microlubrification pour l’usinage industriel
Réduction drastique de la consommation de lubrifiant
-
La microlubrification permet de n’utiliser que la quantité strictement nécessaire de lubrifiant (de 0,04 à 4,2 l/h par buse), contre plusieurs dizaines de litres par heure avec les systèmes conventionnels.
-
Moins de lubrifiant à acheter, à stocker, à recycler ou à éliminer.
Ateliers et process plus propres, plus sûrs
-
Absence d’eau au sol, pas de formation de boues, ni de fonges ou bactéries.
-
Les pièces usinées sortent propres, sans nécessité de dégraissage ultérieur : suppression de l’étape nettoyage dans le process
-
Les lubrifiants adaptés à la MQL sont le plus souvent non dangereux, ininflammables et non toxiques.
Amélioration de la qualité d’usinage et de la durée de vie des outils
-
Application ciblée du lubrifiant, réduction de la friction et de l’échauffement.
-
Usure des outils ralentie, vitesses de coupe et de rotation augmentées.
-
Suppression des phénomènes de collage de copeaux, meilleure évacuation des particules.
Économies d’énergie et de maintenance
-
Suppression des pompes haute pression, déshuileurs et systèmes de filtration lourds.
-
Moins de temps passé à nettoyer les machines et à gérer les déchets.
-
Les centrales de microlubrification sont simples à entretenir : nettoyage du réservoir, purge d’air, remplacement des filtres.
Un atelier aligné avec les exigences RSE et environnementales
-
Réduction de la consommation d’énergie et de ressources.
-
Diminution de l’empreinte carbone et des rejets polluants.
-
Conformité renforcée avec les réglementations environnementales et les politiques de développement durable.
Panorama des centrales de microlubrification : modularité et adaptabilité
Une solution pour chaque besoin
La gamme des centrales de microlubrification couvre tous les besoins, du poste manuel à la ligne de production automatisée :
Modèle de centrale |
Capacité du réservoir |
Nombre de buses |
Type de fluide accepté |
Applications principales |
Mini-TC |
1 L |
1 |
Jusqu’à 100 mm²/s |
Poste individuel, perçage, sciage |
TCJ |
2,5 à 25 L |
1 à 12 |
Jusqu’à 100 mm²/s |
Usinage CNC, emboutissage |
NDJ |
5 L (inox) |
1 à 6 |
Jusqu’à 100 mm²/s |
Lubrifiants plus visqueux |
Profikompakt |
1 L |
1 |
Jusqu’à 100 mm²/s |
Sciage, taraudage, perçage |
PPJ |
1 à 5 L (alu/inox) |
1 à 6 |
Jusqu’à 2 300 mm²/s |
Fluides épais, multi-buses |
MDJ |
10 à 15 L (inox) |
Jusqu’à 60 |
Jusqu’à 2 300 mm²/s |
Grandes installations, automatisme |
Les centrales sont modulaires, adaptables à chaque process et à chaque espace, avec des options de buses, de doseurs goutte-à-goutte, de supports magnétiques, de remplissage automatique, etc.
Facilité de mise en œuvre et d’entretien
-
Installation rapide, fixation murale ou sur machine.
-
Réglage précis du débit d’air et de lubrifiant.
-
Entretien simplifié : vidange, nettoyage du réservoir, purge d’air automatique, filtres accessibles.
Les lubrifiants pour la microlubrification : performance et sécurité
Des formulations adaptées à chaque application
Les lubrifiants MQL sont spécialement développés pour offrir un pouvoir lubrifiant élevé, une évaporation rapide et une absence de résidus gênants. On distingue plusieurs familles :
-
Samnos : base aqueuse, ininflammable, sans pictogramme de danger, excellent refroidissement, anticorrosion, idéal pour l’aluminium et l’acier.
-
Survos : lubrifiants vanescents, haute performance, sans résidus, approuvés FDA, parfaits pour cycles courts et pièces devant rester propres.
-
Sentos : haut pouvoir lubrifiant, très faible résidu, évaporation rapide, conforme aux normes alimentaires.
-
Power & Econi : lubrifiants spéciaux pour la lubrification interne, usinage de matériaux difficiles, très faible quantité résiduelle.
Sécurité et stockage
-
Stockage facilité, longue durée de vie (jusqu’à 36 mois pour les huiles, 12 mois pour les bases aqueuses).
-
Pas de risques physiologiques ou dermatologiques avec les formulations modernes.
-
Réduction des risques d’incendie, d’intoxication et de pollution.
Les buses de microlubrification : précision, robustesse et adaptabilité
-
Buses en aluminium, laiton ou acier inoxydable, robustes et compactes, adaptées aux environnements difficiles (fonderies, centrales béton, etc.).
-
Réglage du débit sur la buse, orientation à 360°, extensions possibles pour atteindre les zones complexes.
-
Compatibilité avec tous types de fluides (jusqu’à 2 300 mm²/s), nettoyage et maintenance aisés.
Impacts économiques et environnementaux de la microlubrification
Économies directes et indirectes
-
Réduction des achats de lubrifiant : jusqu’à 90 % d’économie sur la consommation.
-
Diminution des coûts de traitement des déchets : moins de fluides à recycler ou éliminer.
-
Gain de productivité : moins d’arrêts pour nettoyage ou maintenance.
-
Allongement de la durée de vie des outils : baisse de l’usure, moins de remplacements.
Bénéfices environnementaux
-
Moins de pollution : moins de rejets, moins de brouillards d’huile, moins de risques pour l’environnement.
-
Atelier plus sain : meilleure qualité de l’air, moins d’émanations toxiques, réduction des risques pour la santé des opérateurs.
-
Conformité réglementaire : respect des normes environnementales et des politiques RSE, valorisation de l’image de l’entreprise.
Cas d’usage et applications typiques
-
Usinage CNC, rectification, emboutissage, sciage, taraudage, perçage, fraisage, filetage, polissage, profilage, pliage, extrusion à froid.
-
Adapté à tous les matériaux : aluminium, aciers, inox, titane, matériaux moulés, synthétiques.
-
Intégration possible sur machines individuelles ou lignes automatisées, avec gestion centralisée ou décentralisée des buses.
Réponses aux principaux freins et objections
“La microlubrification est-elle adaptée à mes process ?”
Oui, grâce à la modularité des centrales et à la variété des buses, la MQL s’adapte à tous les types d’usinage, du plus simple au plus complexe.
“Le changement est-il complexe à mettre en œuvre ?”
Non, l’installation est rapide, la formation des opérateurs est simple, l’entretien est réduit. La migration peut se faire progressivement, poste par poste.
“Le retour sur investissement est-il réel ?”
Oui, les économies sur la consommation de lubrifiant, la maintenance et la gestion des déchets sont immédiates. Le gain de productivité et la réduction des arrêts machines accélèrent l’amortissement.
“Y a-t-il des risques pour la qualité des pièces ?”
Au contraire, la MQL améliore la qualité de l’usinage, réduit les défauts de surface et évite la contamination des pièces.
La microlubrification est-elle toujours une option ?
La microlubrification n’est plus une option, mais une nécessité pour qui veut conjuguer performance industrielle, compétitivité et responsabilité environnementale. En adoptant une centrale de microlubrification, vous faites le choix d’un atelier plus propre, plus sûr, plus rentable et prêt pour les défis de demain.
Passez à la microlubrification : faites de l’éco-performance un levier de croissance durable pour votre atelier !
Vous souhaitez aller plus loin dans votre démarche d’optimisation ?
Découvrez notre gamme de centrales de microlubrification sur notre site web Kermaz Pneumatic.
Consultez les autres articles de notre blog.
Contactez nos experts pour des conseils avisés et un accompagnement personnalisé :
✉️ contact@kermaz-pneumatic.com
☎️ 01 69 30 69 80